
V této části seriálu probereme zpracování PUR pryskyřice, nalití do forem, proces přetlakování, vyjmutí odlitků a jejich začištění. Také si budete moci prohlédnout přetlakovou komoru jakou používám a její připojení k ledničkovému kompresoru a nakonec ještě několik praktických rad pro bezpečnou manipulaci s přetlakovou komorou.
косметика оптом в киеве
Základní fáze odlévacího procesu.
Vhodné polyuretanové pryskyřice pro odlévání.
Na trhu je dnes celá řada licích pryskyřic. Abychom se v nich mohli orientovat, je třeba nejdříve vysvětlit jejich některé údaje, které jsou pro nás důležité.
1.Viskozita
Tato hodnota udává jejich tekutost. Čím je hodnota nižší, tím je materiál více tekutý a lépe zatéká do malých dutin formy. Pro detailní odlitky by měla být tato hodnota cca 25-50.
2.Doba zpracování
Je to vlastně čas, po který je od okamžiku smíchání složek, pryskyřice ještě tekutá a dá se lít. Ideální by byla dlouhá doba, třeba 10minut, ale realita je někde jinde. Zpravidla platí, že čím je viskozita nižší, tím je kratší i doba zpracování. U pryskyřic, které jsou vhodné, činí zpravidla 2-6minut. Musíme být tedy rychlí a mít vše velmi dobře připraveno!
3.Doba odformování
Je to nejkratší možná doba, za kterou můžeme odlitek vytahovat z formy. Materiál ještě není úplně vytvrzený, ale už má dostatečnou mechanickou odolnost pro vyjmutí z formy. Musíme si uvědomit, že čím je množství pryskyřice větší, tím je rychlost tvrdnutí kratší. Nejdéle vytvrzuje ve slabých vrstvách. Doba odformování je velmi těsně spjata s dobou zpracování a čím je jedna delší, tím je i delší druhá. U pryskyřic, které jsou vhodné, se pohybuje mezi 20-60minutami.
4.Tvrdost
Tento parametr zase udává, jak je tvrdý materiál po úplném vytvrzení. Většinou se udává ve stupnici „Shore“ a značí se „D“. Zpravidla se tato hodnota pohybuje okolo 68D - 75D
Vyzkoušené pryskyřice.
Vyzkoušel jsem s úspěchem materiály od firmy Axson (F) a Sika (Biresin). Jejich vlastnosti jsou uvedeny v tabulce níže. V současnosti používám Biresin, který je bez zápachu a má i delší garantovanou skladovatelnost.
Materiál |
Viskozita |
Doba zpracování |
Doba odformování |
Tvrdost Shore |
G27LV+G26 |
35 |
2m 15s |
15min |
70D |
F33 |
28 |
2m 10s |
30min |
73D |
F31 |
35 |
1m 50s |
20min |
70D |
F19 |
78 |
8min |
2hod |
72D |
Na co si dát pozor.
Odlévací materiály nejsou zrovna levné a dají se zpravidla koupit v nejmenším balení 1kg+1kg. Garantovaná skladovatelnost je u materiálů Axson 6měsíců, u Biresinu 12měsíců při teplotě mezi 18-23°C. Prakticky se dají použít i po delší době, ale musíme dodržet několik pravidel.
Všechny pryskyřice jsou hygroskopické (pojímají vzdušnou vlhkost) a zvyšující se obsah vody způsobuje tvorbu bublinek při tuhnutí (pěnění) a narušuje vytvrzovací reakci. Je tedy nutné je skladovat ve vzduchotěsných obalech a pro práci si vždy odebírat jen menší množství, které za kratší dobu zpracujeme (několik týdnů). Před odběrem je nutné jednotlivé složky protřepat (kritické je to hlavně u F19). Nádoby od starých pryskyřic nepoužívejte na nové (dolití). Neskladujte při nižších teplotách (v lednici), protože dochází ke krystalizaci a náprava není jednoduchá. U starších materiálů si před použitím vyzkoušejte jejich funkčnost.
Probarvení pryskyřice.
Tento detail se může zdát mnohým zbytečný, ale má své opodstatnění. Vlastní barva pryskyřice po ztuhnutí je velmi světlá, nažloutlá. Velmi špatně na ní vidíme různé kazy, které by bylo vhodné opravit před nástřikem surfaceru. Obarvení také usnadňuje následovnou práci, dolepování detailů atd. Pokud dáme odlitku stejnou barvu, jakou bude potom opatřen, omezíme viditelnost sedření svrchní barvy na hranách (funkční modelařina, pojízdné železniční modely atd.). Na barvení se prodávají zvláštní barvy (Sika - Biresin Farbpasten). Dají se vzájemně míchat, takže nejpraktičtější, šedou, si vyrobíte smícháním bílé a černé do požadovaného odstínu. Jeden kolega používá na probarvení syntetické modelářské barvy (Humbrol, Revell), ale to nemám vyzkoušené a můžete zkusit experimentovat tímto směrem sami.
Odměřování dávky složek.
Každý výrobce udává v technickém listu poměr v jakém se jednotlivé složky míchají. Dodržení tohoto poměru má vliv na rychlost tuhnutí i na mechanické vlastnosti vytvrzené pryskyřice. Ze špatně namíchané pryskyřice se můžou také časem uvolňovat různé sloučeniny a narušovat vrstvu barvy a měnit její odstín.
Mísící poměr bývá udáván v hmotnostních jednotkách, podobně jako u silikonkaučuků. Ale, na rozdíl od nich, jsou měrné hmotnosti obou složek velmi podobné (např. u F33 je to 0.96g/ml a 1.1g/ml). Proto při míchání menšího množství pryskyřice (cca do 10ml) můžeme dávkovat množství objemově. U většího množství bychom už měli odvažovat a nebo si přepočítat hmotnostní objemy na dávku v ml u každé složky.
K odměřování menších množství jsou vhodné plastové injekční stříkačky. Můžeme do nich odebrat pracovní množství složek pryskyřice (kvůli omezení navlhnutí, viz. výše), zazátkovat je uštípnutou a zmáčknutou jehlou a přímo z nich dávkovat. Pro zvýšení přesnosti je dobré přiložit ke stříkačce ustřižený kousek měřítka a odměřovat podle něj a hrany pístu. Pro opravdu malé množství je možné dávkovat kapkami. Zase můžeme přímo ze stříkaček, velmi citlivým stlačováním pístu.
Zpracování polyuretanové pryskyřice.
Zpracování pryskyřice teď probereme krok za krokem s doprovodnými obrázky.
Kvůli omezení „zvlhnutí“ složek, si odebereme menší množství, které stačíme během několika týdnů zpracovat, do injekčních stříkaček a zazátkujeme uštípnutou a zmáčknutou jehlou. Nenecháváme vzduchové bubliny a po spotřebování obsahu použíjte nové stříkačky. I malý kousek staré ztuhlé složky(zvláště tmavé), může způsobit spontánní krystalizaci celého objemu. Pokud používáte více druhů pryskyřice, označte typ na nalepený štítek.
Pro míchání malých množství je ideální plastový „panák“ našikmo přilepený aranžérskou lepící gumou k podložce. Vše lze koupit ve větším papírnictví.
Kelímek můžeme použít mnohokrát. Zbylou pryskyřici necháme ztvrdnout a kelímek pootočíme. Vyhazuji je až po naplnění do poloviny, když už může míchaná pryskyřice vyšplíchnout přes okraj.
Odměříme složku „A“ (světlá, průhledná až mléčná).
Na špičku míchací špejle dáme trochu barvy (viz. výše „Probarvení pryskyřice“). Doporučené množství je max. 2%, ale v takovém malém množství ji nelze přesně dávkovat. Barvu skladujte také ve vzduchotěsném obalu. Osvědčila se mi malá sklenička od medu.
Důkladně promíchejte do směsi s homogenní barvou a zbytek barvy ze špejle setřete.
Odměříme dávku složky „B“ (jantarová) a důkladně promícháme. Dáváme pozor na příliš prudké míchání, které způsobuje vmíchání vzduchových bublin.
POZOR!! Od této chvíle běží čas daný dobou zpracování (obvykle 2minuty). Před tímto krokem si vše pečlivě připravte na další práci (zapnutí kompresoru, příprava tlakové komory, otevření lahvičky s ředidlem pro vypláchnutí aplikační stříkačky atd..), ať se dostane pryskyřice do formy v co nejvíce tekutém stavu!
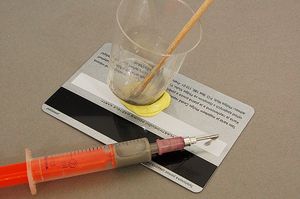
Obsah kelímku nasajte do aplikační stříkačky s tlustou jehlou (1,2mm, růžová) na konci zbroušenou do roviny. Dejte pozor na nechtěné přisátí vzduchu, což vede k tvorbě vzduchových bublin, které můžeme vytlačit do formy. Je lepší raději nenasát vše, až do dna, ale trochu v kelímku nechat.
Plnění forem.
Nejlepší způsob je formu tlakem prstů rozevřít a zasunout aplikační jehlu na nejhlubší místo formy. Musíme se vyvarovat poškození formy o hranu jehly a taky přílišnému zasunutí jehly, kdy se ucpe její konec o formu. Potom pomalu a plynule vytlačujeme pryskyřici do formy, až k úrovni nálitku. Potom jehlu vysunujeme, doplňujeme snižující se hladinu a formu lehkým stiskem zase mačkáme do původního tvaru. Nesmíme to přehnat, jinak si vytlačíme pryskyřici do nálitku a můžeme vcucnout při prudším uvolnění vzduch. Pak doplníme ze stříkačky nálitek.
Zbylou pryskyřici ze stříkačky vymáčkneme do odpadní nádobky a stříkačku i s jehlou ponoříme do skleničky plné ředidla S6300. Tu si před smícháním složek otevřeme. Několikrát nasajeme a vystříkneme ředidlo, při stálém ponoření stříkačky. Tím ji vypláchneme od zbytků pryskyřice a můžeme ji znovu použít. Pokud ztvrdne pryskyřice uvnitř, musíme ji vyhodit a nahradit novou (i jehlu). Stříkačku s nasátým ředidlem necháme v nádobce a později ji očistíme od zbytků ředidla. Pryskyřice totiž dále tuhne a nečeká, až s tím budeme hotovi.
Přetlakování.
Naplněné formy vložíme do přetlakové komory a tu uzavřeme. Začneme plnit na požadovaný tlak. Zde detaily, jak to udělat vynechám, protože bude záležet na konkrétním provedení komory.
Po dosažení max. přetlaku vypneme kompresor a ventilem komoru uzavřeme.
Ponecháme v klidu po dobu, jakou má použitá pryskyřice udanou jako čas „odformování“. Nenechávejte formy pod tlakem uvnitř déle (viz konec kapitoly)!! Za tu dobu by neměl tlak v komoře poklesnout o více než 5%. Musí být tedy velmi dobře utěsněná.
Po příslušné době pomalu vypustíme přetlak z komory a vyjmeme formy. Necháme ještě nějaký čas vytvrzovat (nechávám cca 5-15min, čím členitější odlitek, tím déle).
Nakonec vyjmeme odlitky z formy a můžeme je začistit. Podle typu a umístění nálitku, ho můžeme ulomit, uříznout skalpelem a nebo slabou pilkou. Slabé blanky po řezech a nebo výplních odstraníme skalpelem a přebrousíme. Místo odstranění nálitku zbrousíme pilníčkem, frézkou nebo smirkem. Pokud najdeme místo, kde je bublinka, je nutné ji nejdříve vrtáčkem příslušné velikosti vyvrtat a následně zatmelit a zabrousit. Odvrtání je nutné z toho důvodu, že se nepodaří většinou užším otvorem dostat tmel do celého prostoru, ten udělá spíše tenkou blanku na povrchu a po přebroušení se bublinka objeví znovu.
Ještě bych chtěl upozornit na některé jevy, se kterými se budete moct při tomto způsobu odlévání setkat. Jedná se hlavně o vytvoření bublin v bloku formy při použití velmi měkkého silikonkaučuku (M4615). Tyto bubliny se objeví vždy po odtlakování a zmizí zpravidla za několik hodin až dnů. Vznikají difúzí stlačeného vzduchu do mikrobublinek uvnitř formy, které nejsou v normálním stavu vůbec viditelné a tento vzduch je po odtlakování také „nafoukne“ do viditelných rozměrů. Čím déle je forma pod tlakem, tím větší množství stlačeného vzduchu se do nich dostane, proto neprotahujte dobu přetlakování víc, než je nutné. Pokud formu používáme opakovaně za sebou, tak tyto bublinky nevadí, protože se při opětovném natlakování zase zmenší a odlitek tedy není deformován. U tvrdších silikonkaučuků (M4600) se tento jev objevuje zřídka.
Další jev, který můžeme pozorovat při rychlém vypuštění vzduchu z komory je tzv. „zamžení“. Při prudkém poklesu tlaku dojde k ochlazení vzduchu uvnitř komory a kondenzaci vzdušné vlhkosti. Je tedy vhodné vypouštět vzduch pomalu.
Jako poslední a velmi pozitivní jev, je zabránění nebo minimalizace tvorby bublinek v navlhlé polyuretanové pryskyřici. Lze tak zpracovat i materiály, které se při vytvrzování v normálním prostředí promění v porézní i uvnitř odlitku. To výrazně prodlužuje dobu použitelnosti pryskyřice a šetří naše prostředky. Samozřejmě, pokud už nenastartuje vytvrzovací reakce a pryskyřice nevytvrdne, tak už ani použití přetlaku tento stav nezmění.
Přetlaková komora.
Předně bych chtěl upozornit, že toto zařízení musí splňovat všechny náležitosti dané předpisy pro výrobu, zkoušení a provoz tlakových zařízení. Autor článku ani redakce nemůže nést odpovědnost za škody na zdraví a majetku vzniklé v důsledku používání takového zařízení, vyrobeného na základě informací z tohoto článku. Pracovní tlak 1MPa (10atm) představuje namáhání 10kg na jeden centimetr čtvereční. Plocha 10x10cm je tak namáhaná silou, odpovídající hmotnosti 1000kg!! Případná exploze může způsobit vážnou újmu na životě a majetku.
Přetlaková komora, jako klíčové zařízení, musí splňovat několik kritérií. Jednak musí s dostatečnou rezervou vydržet pracovní tlak. Dále musí jít velmi snadno a rychle otevřít a uzavřít, abychom zbytečně neztráceli čas a pryskyřice ve formách neztuhla a nakonec musí mít přizpůsobený objem k výkonu kompresoru, aby se komoru podařilo natlakovat na pracovní tlak do jedné minuty.
Komora kterou používám je vyrobená z filtru na vodu. Je vyzkoušená na přetlak 1,5MPa (15 atm) a pracovní tlak je 1MPa (10atm). Vnitřní objem je cca 1litr, lze ji rozšroubovat a sešroubovat, díky závitu s velkým stoupáním za velmi krátký čas. Dovnitř jsem vyrobil dvě poličky s alternativním umístěním, jednu pro objemnější a vyšší formy, druhou pro více malých a nebo nižší a větší formy. Všechny armatury jsou vodovodní, ventily jsou kulové a pro utěsnění je použitá instalatérská teflonová páska, které musíme dát dost silnou vrstvu. Těsnost musí být taková, aby za 30minut nedošlo k víc jak 5% ztrátě tlaku. Tlakový systém musí obsahovat manometr a pojistný ventil. Ten můžeme také použít vodovodní, na jmenovitý tlak, a zařadit ho mezi kompresor a ventil komory (kvůli možnému úniku tlaku). Z vlastní zkušenosti mohu potvrdit jeho důležitost, protože mi už nejednou zachránil komoru před přetlakováním (ledničkový kompresor dá tlak až 30atm). Manometr mám nainstalovaný přímo na komoře a má rozsah do max. tlaku, ale při tlakové zkoušce jsem ho musel nahradit jiným, s rozsahem do 1,5násobku tlaku (tento by se tak vysokým tlakem zničil). Tlakovou zkoušku jsem prováděl vodou, aby se v případě roztržení nemohly úlomky rozletět (voda je na rozdíl od vzduchu nestlačitelná a není v ní tedy ani nakumulovaná žádná energie).
Přetlaková komora z vodního filtru.
Gumové těsnění je namazané silikonovou vazelínou pro zvýšení těsnosti a pro lepší držení v drážce.
Na výstupu filtru je pomocí instalatérských redukcí nainstalován manometr. Vhodnější je použít typ do max. zkušebního tlaku.
Na vstupu do nádoby jsou dva kulové ventily. Jeden (více vlevo) uzavírá vstup do nádoby, druhý se otevře při vypouštění komory, aby mohl vzduch uniknout ven.
Tělo nádoby s nalepenými zarážkami pro poličku na formy.
Polička na vysoké formy je udělaná z víčka od zavařovací lahve.
Druhá polička je z kusu tvrdého plastu a zasune se do vyříznuté drážky.
Hadice ke kompresoru je vodní vysokotlaká a v místě připojení je vyplněná papírovým kapesníčkem. Ten zabraňuje průniku oleje z kompresoru do hadice a nádoby.
Na výstupní trubku kompresoru je připájená redukce na půlpalcový závit. Trubka je nejdříve omotaná mosazným slabým plechem, aby bylo nasunutí redukce těsné a potom je vše zapájeno cínem. Pro pájení je vhodné použít agresívní pájecí kapalinu a vše potom opláchnout.
Mezi toto spojení jsem vložil pojistný ventil (není na obrázku).
Tlakování komory bez něj je životu nebezpečné!
Celá sestava ještě bez pojistného ventilu.
Závěr.
Děkuji všem trpělivým čtenářům, kteří se propracovali celým seriálem až sem. Doufám, že Vám tyto informace poslouží k obohacení modelářské tvorby a zjednoduší výrobu různých vlastních doplňků. Sice jsem se snažil vše nastínit alespoň trochu přehledně, ale nejsem si jist, že se to všude úplně povedlo. Pokud budete potřebovat nějaké podrobnější vysvětlení nebo doplnění, tak mě prosím kontaktujte emailem a velmi rád Vám pomohu. Budu se snažit, jak jsem již sliboval, nafotit a popsat výrobu některých složitějších a méně obvyklých odlitků a seznámit Vás s tím, ve formě samostatných článků.
Přeji Vám mnoho úspěchů a radosti při výrobě vlastních odlitků.
Ondřej Nadrchal